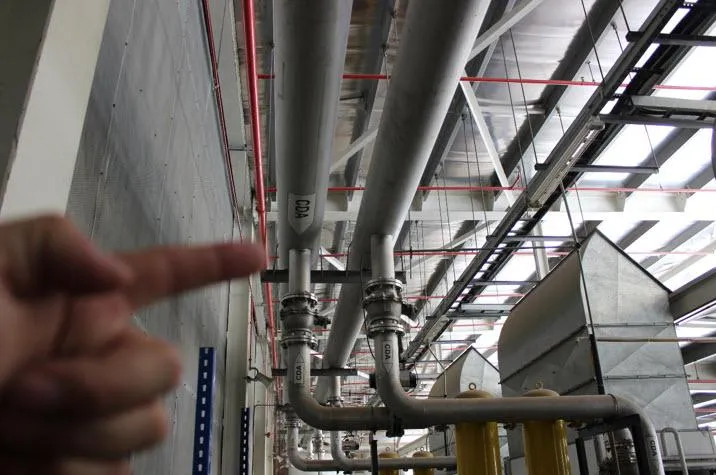
Water Hammer
A building products company chose to allow their piping contractor to design the piping system in their compressor room. Rather than coming off the top of the wet header in the compressor room the compressors were connected to the bottom of the run. This was much simpler and less costly for the contractor and allowed him to finish the job quickly.
Only one of the two compressors at the site ran at a time, the main compressor being a lubricated screw compressor and the backup a reciprocating unit. The piping was arranged in such a way that the compressed air had to flow past the drop to the backup compressor before heading to the dryer.
One day the main compressor needed to be serviced so an attempt was made to start the backup unit. Within seconds the unit failed due to head gasket blowout. It was discovered as the air was flowing past the backup unit's piping drop the entrained water filled the pipe little by little until it was completely full. Some of the water leaked into the backup compressor cylinders, and of course since the water is incompressible head failure was the result.
Even without failure the plug of water expelled by the compressor would have severely stressed the main air dryer input filter and overloaded the dryer. The piping was reconfigured and drip legs with drains installed to prevent further damage.
Learn more about piping in our next Compressed Air Challenge seminar . Visit www.compressedairchallenge.org for more information.