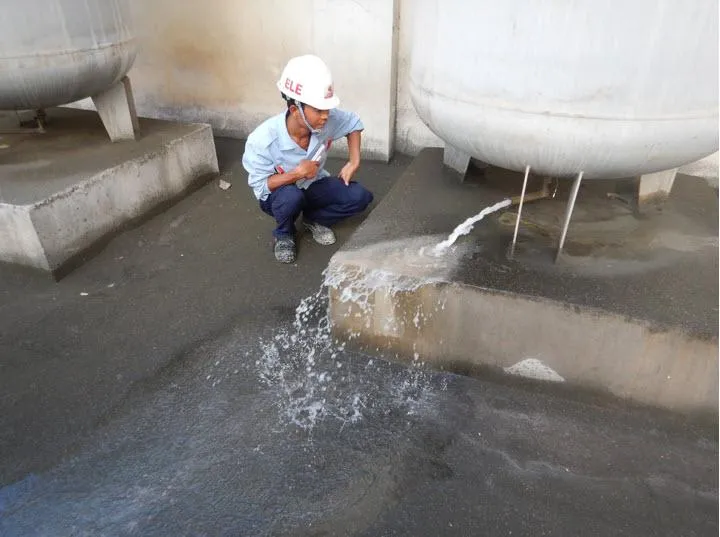
Storage wet or dry?
The answer is yes! Let me explain. Having adequate receiver capacity is very important to both reciprocating and screw compressors to prevent rapid cycling in the load/unload or start/stop condition. As mentioned in a previous blog post having large storage helps make a compressor run more efficiently and extends its lifetime. But a question typically comes up about where to put the receiver; should it be located as wet storage before the air dryer and filters, or should it be placed downstream on the dry side.
Placing a wet receiver right at the discharge of the compressor before the air dryer gives a nice place for the air to cool, allows a quiet zone of low velocity for water and contaminants to drop out, and is the best place for the compressor control. Should the air compressor water separator drain fail, the condensate will simply collect in the bottom of the receiver, rather than swamping the air dryer. Locating the receiver right at the compressor discharge also provides the best solution in terms of reducing compressor cycling because the compressor can "see" the whole "effective storage". More about effective storage later. A disadvantage of having all the storage upstream of the air dryer has to do with the capacity of the dryer. Air dryers are typically sized around the same capacity as the air compressor. But, if large peak demands must be serviced that occasionally exceed the capacity of the air compressor, some air will come from the storage receiver and add to the full output of the compressor. This might mean the dryer would be overloaded beyond its capacity and allow moisture to pass to the dry side of the system.
Placing the system storage downstream of the dryer prevents this from happening, the stored air is pre-dried and pre-filtered, and there is no peak loading on the dryer. But this leaves no place for excess temperature and water to be removed before reaching the dryer. Also, the pressure drop across the air dryer and filter makes the storage less effective in reducing compressor cycles. If, for example, the compressor is set for a 10 psi pressure band, the dryer pressure differential is 4 psi, and the filter differential is 3 psi, the combined pressure differential of 7 psi leaves only 3 psi of pressure swing at the receiver. This makes the receiver capacity less effective by a factor of 3/10ths, meaning the compressor cycles would be more than three times more frequent. In essence the compressor only "sees" a receiver less than one third the size because it must "look" through the dryer and filter.
The best situation is to have both wet and dry receivers. Situate a receiver about 1/3rd the required size as wet storage and 2/3rds downstream of the dryer as dry storage. And if the compressor is capable of remote sensing (some are not), situating the pressure sensor on the dry receiver will assist with preventing the pressure differential problem from reducing storage effectiveness(this must be done carefully ensuring the compressor does not overpressure). It will also give you better pressure regulation through changing conditions.
Having both wet and dry receivers takes some of the peak load off the dryer because the flow is averaged to some degree, which is of additional benefit. Of course, the receivers should be equipped with efficient airless drains and proper pressure relief valves as per safety requirements.
Learn more about storage here: www.compressedairchallenge.org/calendar