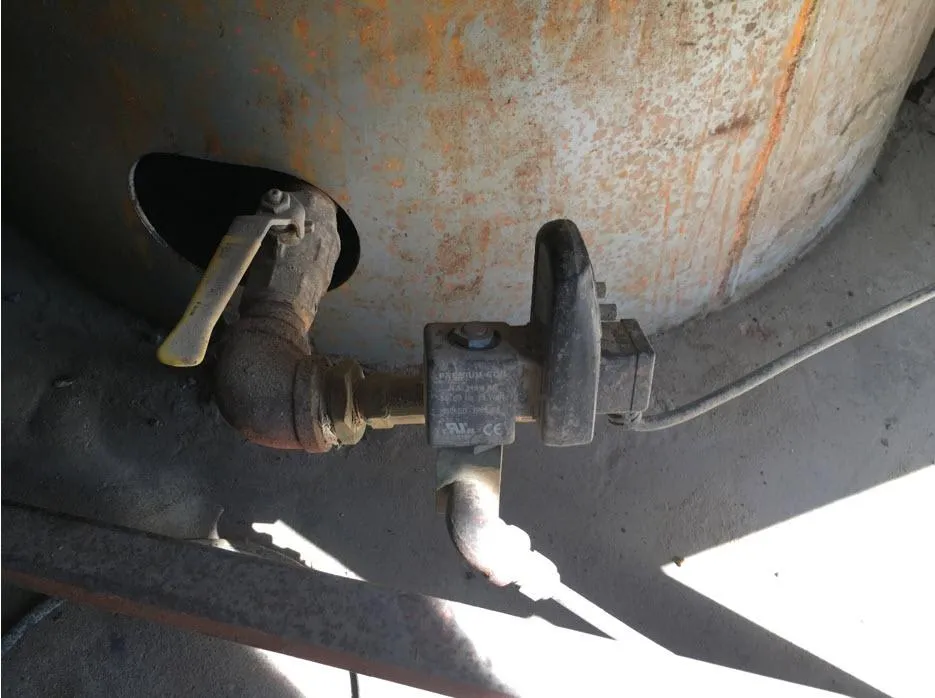
Lack of Maintenance
A small wood products company was hesitant at first, but after some prodding they allowed a compressed air auditor to have a look at their compressed air system. Instruments were placed on the single air compressor and a flow meter installed. Pressure loggers measured the compressor discharge and plant pressure.
When the data was analyzed the auditor found that the air compressor was only 20% loaded, yet the air compressor was consuming 76 percent of its full load power. The air pressure swung wildly as tools and equipment were used to assemble their product. The auditor calculated the energy consumption and found that the air compressor and dryer were consuming about 50% of the total facility energy consumption. To top it off about half of the compressor output flow was to feed leaks.
The auditor noticed that a pail beside the drain on the dry receiver tank was completely full of water. A check of the air dryer showed it was working, but the condensate drain, installed internally, had failed, but this had not been noticed. Water was being allowed to enter the plant, luckily a receiver drain captured the excess.
The company's compressed air service provider had not been monitoring the operation of the compressor controls or dryer during their maintenance. The compressor inlet valve had failed partly closed causing poor efficiency and inadequate pressure control. They hadn't bothered to check the operation of the dryer drain.
The auditor calculated that repair of the compressor and repair of their leaks could save 40% of their existing compressor electrical consumption. But this company did one better, since the compressor was at the end of its life they decided to replace the unit with a VSD compressor, saving 60% and gaining a substantial energy rebate.
Learn more about system optimization in our next Compressed Air Challenge seminar in your area. Visit www.compressedairchallenge.org for more information.