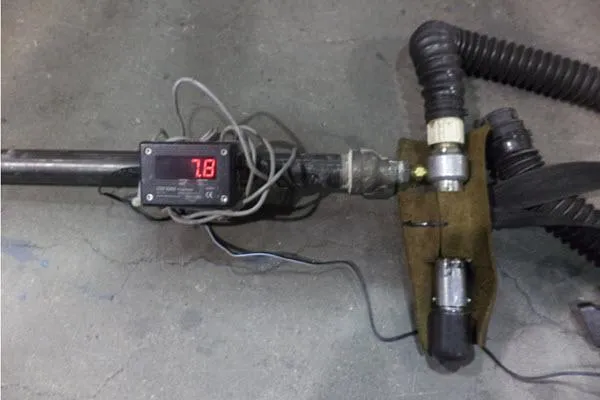
How do I measure leaks
If yours is like most compressed air systems there is usually no simple way of directly measuring leaks. Most air compressors have no flow gauge installed for you to read. But a good rough estimate can be done by indirectly measuring during some special testing using a watch and determining the flow using a calculator.
If your air compressor loads and unloads, or starts and stops during its normal operation do this simple test when there is no production running in the plant, one compressor is running, and all known air demands that are not leaks are turned off:
Figure out when the compressor loads (the pressure starts to go up) and time the load cycle with your watch, and then time following unload cycle, repeat this five times while recording the number of seconds for each cycle,
Calculate the average the number of seconds the compressor was loaded during all the tests, and do the same for the number of seconds unloaded.
Calculate by dividing the average number of loaded seconds by the total average cycle time (loaded plus unloaded) and then multiply the result by 100. The answer is the duty cycle of the compressor. For example 15 seconds loaded and 60 seconds unloaded calculates as follows; 15/(15+60)*100 = 0.20.
The find out the output capacity of the compressor, it sometimes says on the nameplate, or definitely in the instruction manual. This capacity is usually roughly the nominal hp times 4. For example a 30 hp compressor with output pressure of around 120 psi would have a capacity of 30*4 = 120 cfm. Multiply the duty cycle times the compressor capacity and you have your average leakage flow. So for example 120 cfm * 0.20 = 24 cfm leakage.
For compressors that don't load and unload, like units that run in modulation mode, you can simulate load and unload by stopping the compressor and timing how long it takes for the pressure to fall 20 psi. Then start the compressor and time the 20 psi rise, make sure the compressor is always fully loaded for this pressure rise (this is sometimes tricky). Then use the same calculation method as just described.
If your plant never shuts off then things are more difficult for you, but hunting for leaks and fixing them is all the more rewarding because of higher operating hours. In this case you can do the special testing on plant shutdowns as just described. If there are no plant shutdowns, then testing with an ultrasonic flow meter is the best option.
Secondary flow metering can measure these leaks if they can be isolated. Ultrasonic leak detectors can be rented from local compressed air suppliers. Sometimes the suppliers will even come and do a survey for you.
For plants that run 8,760 hour per year the reduction of just 20 cfm of leaks can typically save you $3,500 in electrical costs per year at 10 cents per kWh. This level of leaks can be found in about an hour in most large industrial plants. A good hourly wage if you can get it!
An easier method would be to purchase a flow meter for your plant and install it in your main header. There are many suppliers of thermal mass flow meters that can measure the flow of dry air during leakage testing so you can know without any calculation. These meters can also be used to track your flow profile if hooked up to a recorder, something that could help you track your total compressed air consumption. This, coupled with energy sub-metering can be used to calculate and track your compressed air system efficiency.
Learn more about leaks at our training www.compressedairchallenge.org/calendar