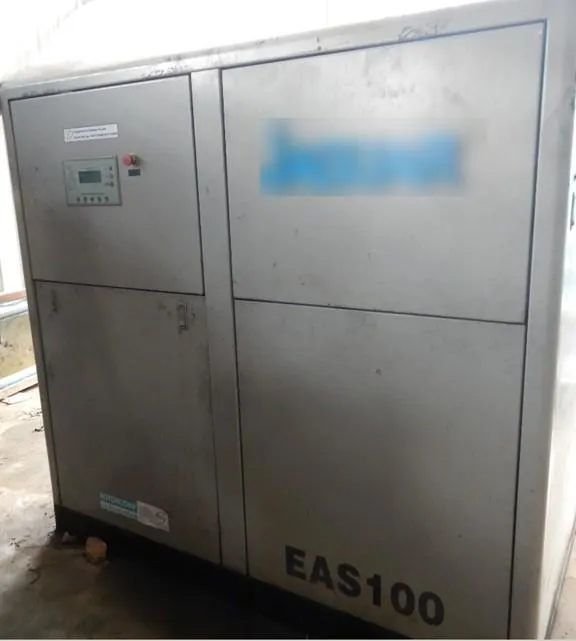
How do I make my compressed air system more efficient?
There are three important basic "secrets" to making your compressed air system more efficient. These are
Produce the compressed air more efficiently,
Waste less compressed air,
Use the compressor heat for something useful.
To produce the compressed air more efficiently the work to improve things is mostly done in the compressor room. For systems with lubricated screw compressors the most important item to address is compressor control. These kind of compressors need lots of storage receiver capacity and properly coordinated control, especially if more than one compressor will be running at a time. Also, making improvements to piping, filters, dryers and other components can reduce pressure restrictions and allow the compressor discharge pressures to be lowered, saving energy. Here is a partial list of common efficiency improvement measures:
Install large storage, if you have less than 5 gallons per cfm output of the trim compressor then your tanks are likely too small,
Adjust the compressor control for proper coordination and set to automatically turn off when compressor not required, this may require the help of a service specialist,
Lower compressor discharge pressure, this needs to be done carefully to avoid problems in the plant, "
Reduce filter and piping pressure differential by proper design and upsizing,
Reduce or eliminate any condensate drain compressed air waste,
Use efficient air dryers, cycling refrigerated, or, if desiccant style types with dew point control to save purge,
Use variable speed or variable capacity compressor control,
Purchase a more efficient compressor than the existing unit, compressor design has been improved in recent years,
Turn off your system when not required, like during evenings or weekends,
Improve the compressor room environment so cool clean air is ingested by the compressor, using cool outside air will increase efficiency,
Have a compressed air audit done to detect efficiency problems.
To reduce the flow of compressed air most of the required work needs to be done in the plant. This involves thoroughly searching the plant for any devices or conditions that might be causing wasted flow, leakage, or things that should be switched to some alternative energy source besides expensive compressed air. Some common energy efficiency measures:
Leakage search and repair using hand held ultrasonic detectors, regular monitoring and testing leakage levels is very important,
Measuring piping pressure loss and improving piping and component capacity (filters, regulators, lubricators, connectors, hoses), this allows the compressor pressure to be reduced,
Lowering plant pressures using pressure flow controller, this reduces flow in unregulated devices,
Conversion of inefficient devices to direct electric actuators, motor, low pressure blowers, coolers using compressed air.
Installing shut off valves to reduce compressed air waste on equipment that is not in production but still consuming compressed air.
Have a demand side audit done by an experienced auditor.
Since 90 percent of the energy input to an air compressor comes out as heat, the use of the heat of compression is a very good energy efficiency measure if there is something in the plant that could use the heat rather than using electric or fuel source heating devices. Some common uses of heat:
General plant space heat,
Boiler or hot water heater makeup heat, some compressors can be purchased or retrofitted with water heat exchangers,
Drying of paint,
Air dryer purge (for lubricant free compressors),
Process related heat like heating of chemical treatment tanks,
Heating water on the inlet of RO water treatment (makes the system more efficient).
Putting the three secrets together can help you make your compressed air system more efficient and more reliable.
Check out our training for more information here: www.compressedairchallenge.org/calendar