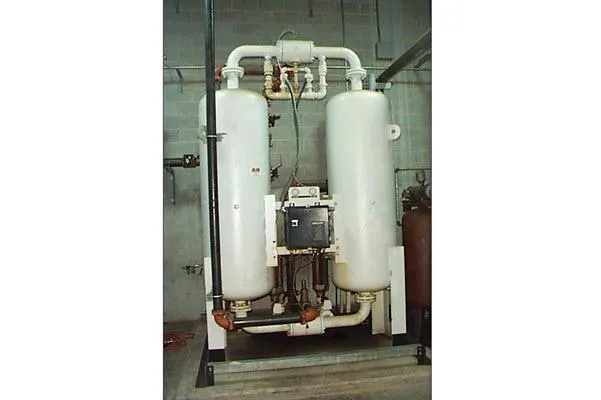
How costly is your desiccant dryer?
Desiccant dryers will consume about 2 to 3 kW of energy for every 100 cfm of dryer rating compared to about 0.8 kW per 100 cfm for refrigerated dryers, almost 4 times as much! But if you have a desiccant style air dryer in lightly loaded conditions it may be costing you more than you think.
These dryers use a bed of desiccant, usually activated alumina, to strip the water molecules from the compressed air to produce a very dry minus 40 dew point flow of air. There are a few different styles of these dryers, ranging from the simplest heatless to the more complex heated blower purge units. The most common is the heatless style.
In these dryers the desiccant can only hold so much moisture before it becomes saturated. In order to provide a continuous flow of dry air, two vessels of desiccant are used, one actively drying the air, while the other runs through a purge cycle that regenerates the desiccant. The dryer will automatically switch sides when required.
It is the regeneration of the desiccant that costs energy, with the purge flow consuming about 15 to 20 percent of the dryer nameplate rating in a heatless unit. The previous words have been emphasized for a reason, in uncontrolled dryers without dew point control, the flow is not 15 to 20 percent of the actual flow, but is a fixed flow based on the dryer rating.
For example, a system with two 220 cfm 50 hp compressors might have an associated air dryer rated at 500 cfm, the next size up because 440 cfm dryers are not available. Perhaps only one compressor normally runs, and its average flow might only be 150 cfm through the normal production cycle. If the dryer was fixed cycle it would consume 75 to 100 cfm of compressed air for purge, which would work out to between 50 and 66 percent of the air produced by the compressor, much higher than required. The cost for this purge alone might be up to $19,000 per year if running continuously using power at 10 cents per kWh.
Sadly, when compressed air auditors do studies on systems with desiccant air dryers they often find the dryer is the biggest compressed air demand in the plant. This might be the case in your plant. Fortunately something can be done about it.
One of the first questions an auditor will ask is why do you need the air so dry, many times, especially in warmer climates, there is no reason to dry to minus 40 levels. A switch to refrigerated air drying can reduce the cost of conditioning the air substantially, especially if a cycling dryer is used that turns its power consumption down in proportion to reduced moisture loading.
If it is determined you actually need a desiccant dryer there are a few things that should be considered to help reduce operating costs:
· Use dew point control, most desiccant dryers, even small ones have an option to install a moisture sensor that will automatically reduce the cost of desiccant regeneration in proportion to the moisture loading. For lightly loaded systems this can quickly pay back the initial cost.
· If you already have dew point control ensure it is actually turned on and is operating correctly.
· Ensure the purge flow is adjusted properly and that the dryer valves are in good working order. An erroneous turn of an adjustment valve can cost significant extra energy.
· Right size your dryer, often the dryer is too large for the actual system. In the example above if the system had two dryers of 250 cfm size, one could turn off with the associated compressor.
· Ensure the filter drains associated with your dryer inlet and outlet filters are energy efficient and are not leaking.
· If you are replacing the dryer consider purchasing types that have reduced purge flow, some heated purge or blower purge dryers use very little compressed air (but some electric power). There are some vacuum purge dryers available now that use almost no purge. Some systems can even use waste compressor heat to regenerate. Learn more at our training: www.compressedairchallenge.org/calendar
Le
L